Specifications and Options Automatic Self-Cleaning Strainers
The strainer shall be Model SFA20/SFA30/SFA31 Self-Cleaning, Motorized Type.
The body and cover shall be fabricated (carbon steel), designed, manufactured and tested generally to ASME Section VIII Standards, using qualified ASME Section IX welders.
Housing to be suitable for a design pressure of 150 psig. Inlet and outlet connections shall be flanged and conform to ASME B16.5 standards. The strainer shall have a single backwash connection and drain connections. Unit to be complete with factory supplied steel support legs for bolting to concrete or steel base.
Strainer shall be __________ size capable of handling _________________ gpm of fluid at a _________psig pressure loss with clean straining elements.
The straining element will be manufactured from corrosion resistant (304 Stainless Steel) reverse rolled slotted wedge wire screen designed with ___________ inch openings. The wide or flat cross section of the wedge wire shall face the direction of flow providing for a continuous smooth flat surface to trap debris. The straining media shall be free of pockets, tubes, collector bars, etc. that accumulate and trap debris permanently.
All internal parts will be of corrosion resistant (304 Stainless Steel). The strainer shall be provided with drive shaft and hollow port assembly fitted with all necessary bearings and seals.
The drive arm and hollow port assembly including the adjustable accelerator plate will be free running at a maximum speed of two (2) rpm and not contact with screen surface. Port assembly shall be factory and field adjustable for positive effective cleaning and shear capability.
Note: Sizes 1″ through 16″ have (1) backwash hollow port. Sizes 18″ and up will have (2) backwash hollow ports.
Drive shaft will be supported at the top with roller bearings located in a double reduction gear reducer and at the bottom with a water lubricated guide bearing.
The gear reducer shall be driven by a ____________hp, _______________v, __________ Ph, 50/60 Hz, TEFC motor.
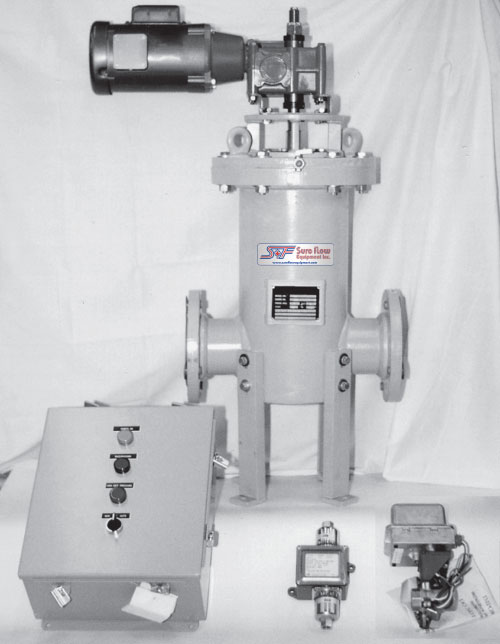
Strainer Options Available
Cover Lift Assemblies – Recommended for remote locations.
ASME – ASME Section VIII, Division 1. 10 CFR 50 Appendix B. ASME Section II, Class 3.
Materials of Construction – Consult factory for stainless steel, copper, nickel, monel, or other requirements.
Control Package – Control Panel with Nema 4 Enclosure, Backwash Valve with Electric Operator, Single Element Differential Pressure Switch.
Design – High Pressure applications – Consult factory.
Spyder-Clean – Low Pressure and Special Application.
Skid Packages – All equipment desired, including strainers, valves, controls, wiring, piping and skids may be combined as a complete, custom package. Size of the project has no limitation.